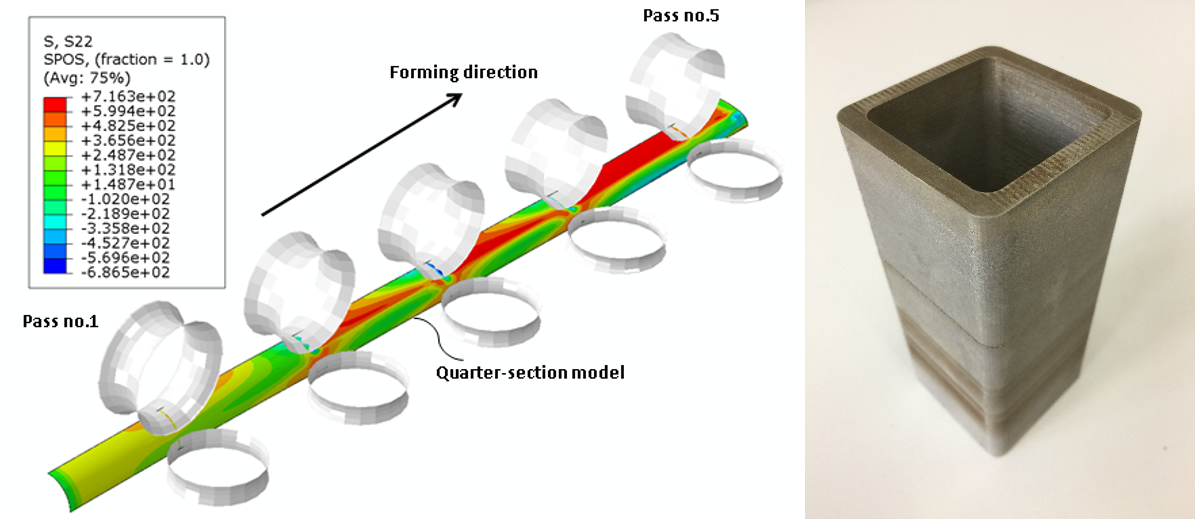
Cold-formed metal structures
No longer a Dream for predicting geometric imperfection, residual stresses and strength enhancement in cold-formed steel structures realistically! A deterministic approach with advanced numerical modeling of manufacturing processes is a solution.
Million tons of cold-formed metal building products are used in construction industry around the world each year. This trend is kept increasing due to their construction efficiency in Modular integrated Construction (MiC). The structural performance of cold-formed thin-walled metal structures is known to be sensitive to initial imperfections which include both geometrical imperfection and cold work due to forming. Traditionally, this cold work effect has been taken into account by using separate specifications of mechanical properties for the flat portions and the corner regions in conjunction with idealized residual stresses models which are based on inappropriate assumptions disregarding the effect of the manufacturing process. Indeed, various cold-formed sections are fabricated by different manufacturing processes (Figs. 1 & 2). Hence, a research has been being carried out to seek for the solution to overcome this shortcoming.
![]() ![]() |
Fig 1. Manufacturing process of roll-formed tubes |
![]() Coiling Uncoiling & Flattening Press Braking |
Fig 2. Manufacturing process of press-braked sections |
Dr. Quach’s research has been focused on the development of various scientific tools (i.e. analytical models, empirical models, and hybrid analytical-finite element approaches) to accurately model manufacturing processes and quantify initial imperfections and the cold work effect (i.e., residual stresses and plastic strains) and in various types of cold-formed members (e.g. channels and hollow sections). The main contribution from this research is to correct the major deficiencies in existing knowledge and existing design approaches by using these proposed tools. The findings confirm the effect of the manufacturing process on the mechanical and structural performance of cold-formed metal members. The proposed methods/tools can be used to predict geometric imperfections, residual stresses and strength enhancement in cold-formed metal structures realistically.
An integration of these proposed scientific tools forms a novel and unified approach for the analysis and design of cold-formed thin-walled structures. This new approach can be used for optimizing the forming parameters of cold-formed steel sections and will greatly reduce the need for laboratory testing in the development of design rules.
The aforementioned research is a large study involving various parts of research, and is conducted through various projects funded by the university and the Fundo para o Desenvolvimento das Ciências e da Tecnologia (FDCT) of Macao S.A.R. This research is being developed at three main directions:
(a) Stress-strain models of thin sheet metals;
(b) Simulations and Predictions for enhanced strengths of cold-worked materials;
(c) Simulations and Predictions for initial imperfections (including geometrical imperfections, residual stresses, plastic strains) in cold-formed members and their effect on structural performance (Figs. 3~8).
![]() |
![]() |
Fig 3. Finite element-based method: Numerical tube forming of EHS tubes |
Fig 4. Advanced finite element approach: Numerical stub column test of EHS |
![]() |
![]() |
Fig 5. Finite element-based method: Numerical press braking |
Fig 6. Advanced finite element approach: Nonlinear buckling analysis |
![]() |
![]() |
Fig 7. Numerically predicted local imperfections in an EHS | Fig 8. FE predicted stub-column behavior of an EHS |
3D printed metal structural members
Additive manufacturing, commonly known as 3D printing, is an evolutional technology in the manufacturing industry. This technology has already been embraced by different industries, such as aerospace and biomedical engineering, and the recent advance in this technology has generated a vast of societal excitement for its future. Despite the exciting prospect of its application in civil engineering, additive manufacturing technology is still at a perceived stage for construction industry. The benefits and potential in construction industry are rarely known in the field at this stage. This research aims to investigate the mechanical properties and structural performance of additively manufactured metal tubular sections (see Figs. 9 and 10). So far, high strength steel tubular stub columns additively manufactured by selective laser melting (SLM) with three different scanning patterns, have been tested. The anisotropy on mechanical properties has been examined through tensile coupon tests in both longitudinal and transverse directions. The influences of scanning patterns on mechanical properties and structural behavior of as-printed high strength steel tubular sections stub columns were also investigated. The test results have been used to assess the applicability of existing design provisions that originally developed for conventionally produced hot-rolled and cold-formed steel tubular sections to the additively manufactured high strength steel tubular sections.
![]() |
![]() |
Fig 9. 3D printing of metals | Fig 10. 3D printed stainless steel tubes |
REFERENCES
(** Research students or Post-Doc from University of Macau. ^Corresponding author)
- Yan, J.J.**, Song, H., Dong, Y.P., Quach^, W.M. , and Yan^, M. (2020), High strength (~2000 MPa) or highly ductile (~11%) additively manufactured H13 by tempering at different conditions, Materials Science and Engineering A, 773, 138845. [Q1 in “Materials science, Multidisciplinary”. Q1 in “Metallurgy & metallurgical eng.”]
- Yao, Y.**, Quach^, W.M., and Young, B. (2019), Cross-section behavior of cold-formed steel elliptical hollow sections – a numerical study, Engineering Structures, 201, 109797. [Q1 in Civil Eng.]
- Cai, Y., Quach^, W.M., and Young, B. (2019), Experimental and numerical investigation of concrete-filled hot-finished and cold-formed steel elliptical tubular stub columns, Thin-Walled Structures, 145, 106437. [Q1 in Civil Eng.]
- Yao, Y.**, Quach^, W.M., and Young, B. (2019), Finite element-based method for residual stresses in cold-formed steel hollow sections, Engineering Structures, 188, 24-42. [Q1 in Civil Eng.]
- Yan, J.J.**, Chen^, M.T.**, Quach, W.M., Yan, M., and Young, B. (2019), Mechanical properties and cross-sectional behavior of additive manufactured high strength steel tubular sections, Thin-Walled Structures, 144, 106158. [Q1 in Civil Eng.]
- Cai, Y., Quach^, W.M., Chen, M.T., and Young, B. (2019), Behavior and design of cold-formed and hot-finished steel elliptical tubular stub columns, Journal of Constructional Steel Research, 156, 252-265. [Q1 in Civil Eng. Q1 in Construction & Building Technology.]
- Yan, J.J.**, Zhou, Y.H., Gu, R.N., Zhang, X.M., Quach^, W.M. , and Yan^, M. (2019), A comprehensive study of steel powders (316L, H13, P20 and 18Ni300) for their selective laser melting additive manufacturing, Metals, 9(86), pp.1-20. [Q1 in Metallurgy & Metallurgical Eng.]
- Abambres^, M., and Quach, W.M. (2016), Residual Stresses in Steel Members: A Review of Available Analytical Expressions, International Journal of Structural Integrity, 7(1), pp.70-94. [Q3 in Civil & Structural Eng. Q3 in Mechanical Eng., according to SJR.]
- Quach, M., and Young^, B. (2015), Material properties of cold-formed and hot-finished elliptical hollow sections, Advances in Structural Engineering, 18(7), pp.1101-1114. [Q2 in Civil & Structural Eng. Q2 in Building & Construction, according to SJR.]
- Quach^, M., and Huang**, J.F. (2014), Two-stage stress-strain models for light-gauge steels, Advances in Structural Engineering, 17(7), pp.937-949. [Q2 in Civil & Structural Eng. Q2 in Building & Construction, according to SJR.]
- Quach^, M., and Qiu**, P. (2014), Strength and ductility of corner materials in cold-formed stainless steel sections, Thin-Walled Structures, 83, pp.28-42. [Q1 in Civil Eng.]
- Quach, W. M., Teng^, J. G., and Chung, K. F. (2010), Effect of the manufacturing process on the behaviour of press-braked thin-walled steel columns, Engineering Structures, 32, pp.3501-3515. [Q1 in Civil Eng.]
- Quach, W. M., Teng^, J. G., and Chung, K. F. (2009), Residual stresses in press-braked stainless steel sections – I: Coiling and uncoiling of sheets, Journal of Constructional Steel Research, 65, pp.1803-1815. [Q1 in Civil Eng. Q1 in Construction & Building Technology.]
- Quach, W. M., Teng^, J. G., and Chung, K. F. (2009), Residual stresses in press-braked stainless steel sections – II: Press-braking operations, Journal of Constructional Steel Research, 65, pp.1816-1826. [Q1 in Civil Eng. Q1 in Construction & Building Technology.]
- Quach^, W. M., and Qiu, P. (2009), Accurate prediction of mechanical properties for cold-formed stainless steel section, Journal of Yantai University, Natural Science and Engineering Edition, 22(3), pp.217-228.
- Quach, W. M., Teng^, J. G., and Chung, K. F. (2008), Three-stage full-range stress-strain model for stainless steels, Journal of Structural Engineering, ASCE, 134(9), pp.1518-1527. [Q1 in Civil & Structural Eng. Q1 in Building & Construction, according to SJR.]
- Quach^, W. M., Teng, J. G., and Chung, K. F. (2007), Finite element predictions of residual stresses in cold-formed steel sections, Progress in Steel Building Structures, 9(3), pp.26-32.
- Quach, W. M., Teng^, J. G., and Chung, K. F. (2006), Finite element predictions of residual stresses in press-braked thin-walled steel sections, Engineering Structures, 28, pp.1609-1619. [Q1 in Civil Eng.]